Discover the Latest Technologies in Metal Stamping for Precision Manufacturing
Discover the Latest Technologies in Metal Stamping for Precision Manufacturing
Blog Article
Advanced Techniques in Metal Stamping for Accuracy Production
As industries consistently demand finer tolerances and complex layouts in their metal elements, the pursuit for advanced methods in steel stamping has escalated. From the usage of advanced multi-stage marking processes to the combination of sophisticated automation technologies, the landscape of metal stamping is going through an extensive change.
Advanced Multi-Stage Stamping Procedures
Discussing the complexities of sophisticated multi-stage marking procedures discloses the innovative strategies employed in modern manufacturing practices. Metal Stamping. Multi-stage stamping is a complicated procedure that involves multiple steps to transform a flat sheet of steel into a final stamped product. Making use of modern dies, where different operations are executed at each stage of the stamping procedure, permits high accuracy and performance in the manufacturing of complex steel parts
During the initial stages of multi-stage marking, the level steel sheet is fed right into the marking press, where a series of dies are used to cut and shape the product. Succeeding phases include additional creating, flexing, and punching operations to more fine-tune the part. Each stage is thoroughly created to develop upon the previous one, causing the development of complex geometries with limited resistances.
Advanced multi-stage marking procedures need a high level of competence and precision to ensure the top quality and uniformity of the stamped parts. By utilizing innovative machinery and tooling, producers can create a vast range of metal parts with effectiveness and accuracy.
Accuracy Tooling Innovations
Precision tooling technologies have changed the metal stamping industry, improving efficiency and high quality in making processes. CNC systems allow for complex styles to be translated directly right into tooling, making certain accuracy and repeatability in the stamping process.
Furthermore, the integration of sensors and real-time tracking abilities in precision tooling has enabled makers to identify and address issues promptly, minimizing downtime and decreasing scrap prices. By incorporating clever innovation into tooling, operators can enhance specifications such as pressure, speed, and alignment during the marking procedure, causing enhanced product high quality and enhanced productivity.

Automation in Steel Stamping
The advancement of accuracy tooling advancements in the metal stamping sector has actually led the means for considerable improvements in automation, transforming the manufacturing landscape towards enhanced efficiency and productivity. Metal Stamping. Automation in steel stamping involves making use of advanced machinery and robotics to carry out various jobs generally brought out by human operators. This change towards automation supplies various advantages, consisting of improved accuracy, quicker manufacturing cycles, and lowered labor expenses
One key facet of automation in steel marking page is the execution of computer mathematical control (CNC) systems, which allow accurate control over the marking process. CNC technology permits the creation of facility and complex steel get rid of consistent high quality. Additionally, automated systems can be configured to run continuously, causing higher outcome rates and shorter preparations.
Furthermore, automation boosts work environment safety and security by decreasing hands-on handling of heavy products and minimizing the risk of crashes (Metal Stamping). As producing markets remain to embrace automation, the future of metal stamping holds terrific assurance for even greater effectiveness and innovation
High-Speed Stamping Techniques
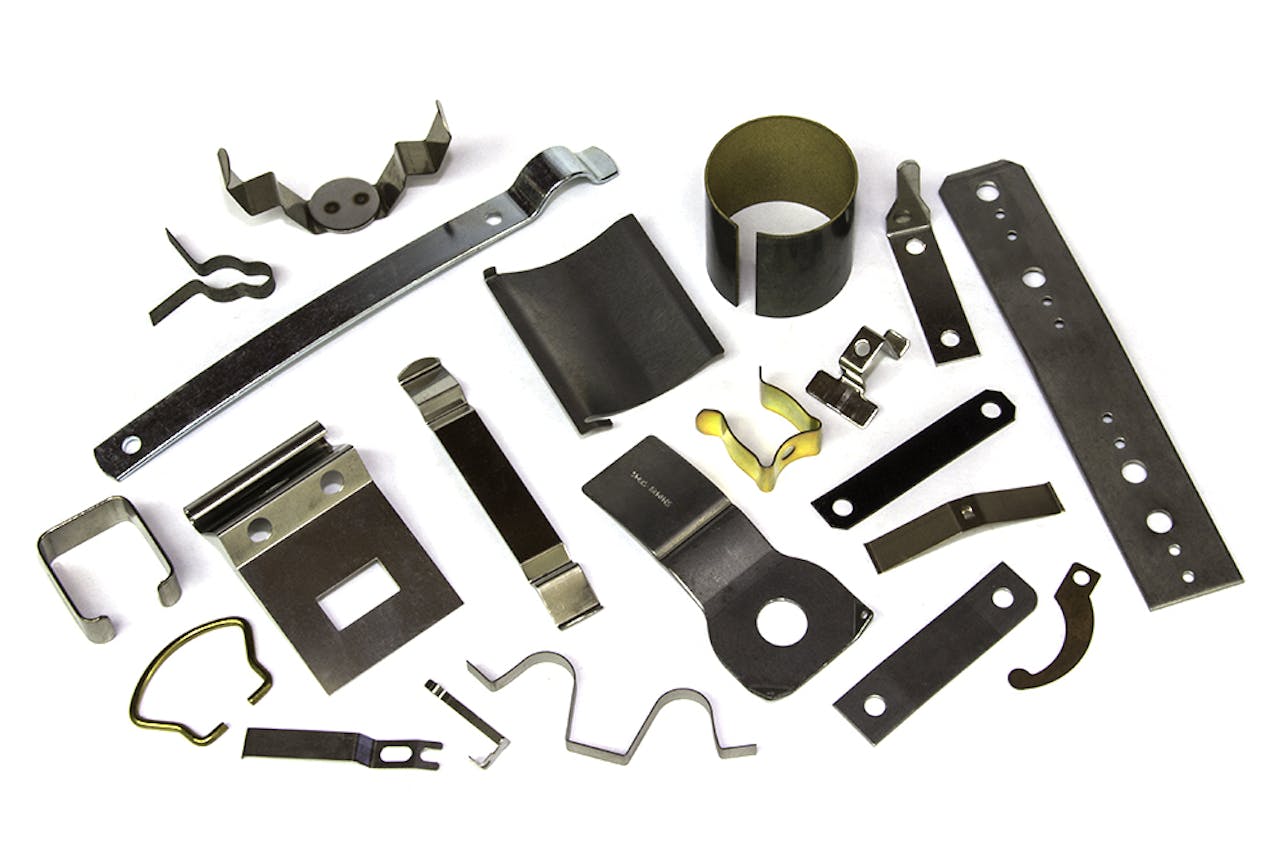
Among the key advantages of high-speed stamping techniques is the ability to create a large quantity of components in a much shorter amount of time compared to conventional stamping methods. This enhanced efficiency not only have a peek at these guys enables producers to satisfy limited production due dates however likewise allows expense savings through economic situations of range. In addition, high-speed marking can help in reducing product waste by enhancing the product use during the stamping process.
Furthermore, high-speed marking strategies commonly integrate cutting-edge features such as fast die adjustment systems and real-time monitoring abilities, additionally explanation improving the general efficiency and adaptability of the steel stamping process. As technology remains to breakthrough, high-speed marking is expected to play an essential role in driving the future of accuracy production.
Quality Control in Stamping Workflow
Effective quality assurance procedures are vital for guaranteeing the integrity and consistency of steel marking operations. Quality assurance in stamping procedures includes a collection of organized processes targeted at finding and avoiding issues in the produced components. One critical element of quality assurance in metal marking is the use of innovative evaluation strategies such as optical assessment systems and coordinate measuring equipments (CMMs) to verify the measurements and tolerances of stamped parts.
In addition, quality assurance procedures in marking operations often include the application of analytical process control (copyright) methods to check the production process in real-time and make certain that it remains within acceptable limitations. By analyzing data and recognizing trends, producers can proactively resolve any discrepancies from the preferred high quality requirements.
Moreover, quality assurance in metal stamping operations likewise includes comprehensive material screening to ensure that the raw materials utilized satisfy the called for requirements for the stamping procedure. This may include conducting material firmness tests, tensile toughness tests, and dimensional evaluations to ensure the high quality and stability of the stamped parts. On the whole, applying robust quality assurance procedures is critical for attaining high-quality stamped components consistently.
Verdict
Finally, advanced techniques in steel marking play a crucial duty in accuracy production processes. Through multi-stage stamping procedures, cutting-edge tooling remedies, automation, high-speed methods, and extensive high quality control steps, producers can achieve greater degrees of accuracy and efficiency in their procedures. These innovations in steel stamping technology have actually made it possible for business to produce intricate get rid of tight tolerances, inevitably causing enhanced item top quality and client satisfaction in the production market.
Report this page